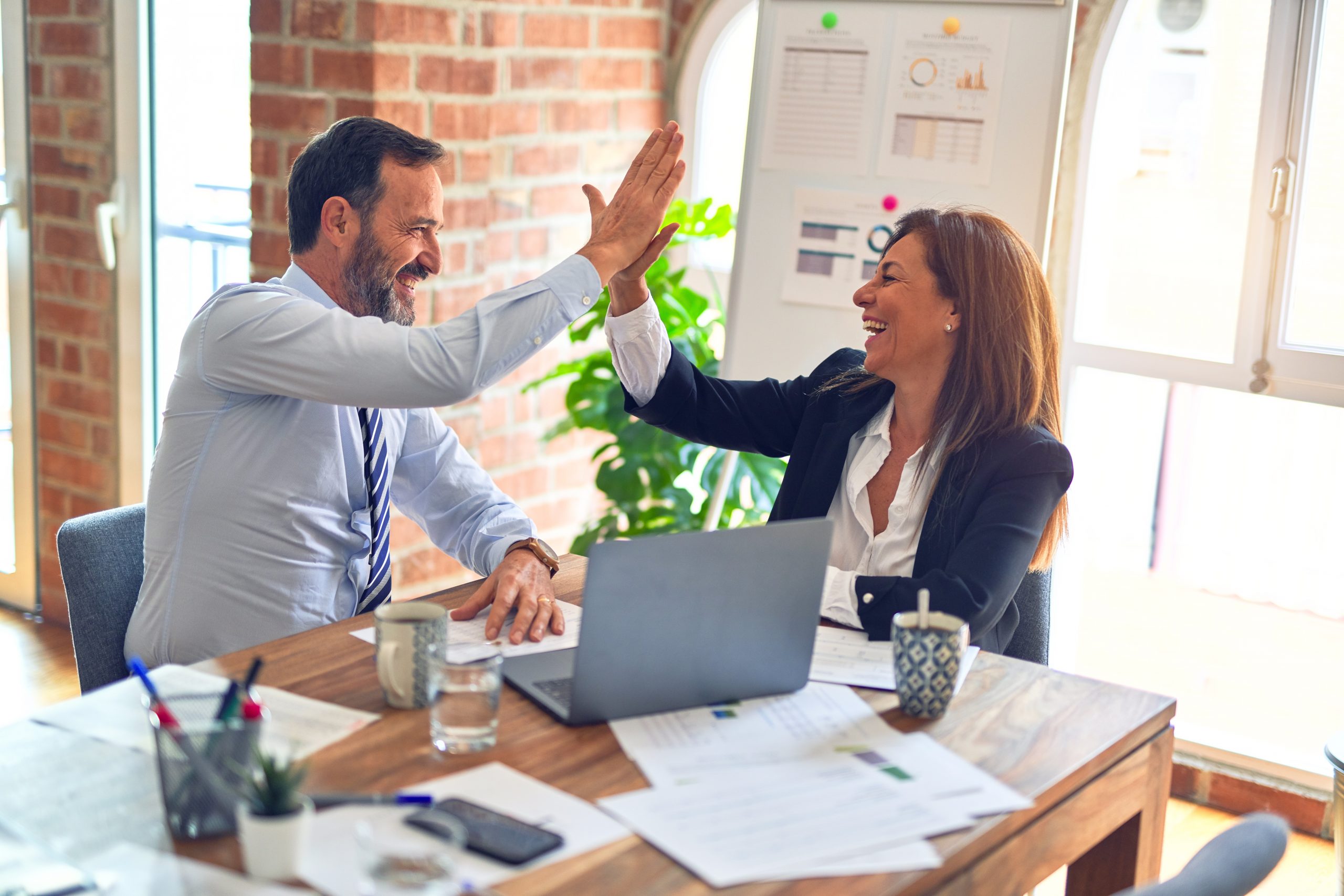
A Lean Six Sigma program – like all change in an organization – is a dynamic process and needs to be systematically and objectively reviewed for opportunities to improve. Continuous process improvement is applicable to the Lean Six Sigma deployment in the same way it is to other processes in the organization. Even companies with several years of Lean Six Sigma experience can experience ebbs and flows in the quality of their programs.
Lean Six Sigma Programs Need Rigidity/Flexibility
Effective Lean Six Sigma programs need to have both the rigidity to withstand certain changes and the flexibility to adapt to others. Ultimately any program’s success is defined by its ability to contribute in terms of increased revenues, margins and capital utilization. On many occasions a company executing a Lean Six Sigma deployment will collect data, establish metrics and measure the success of a given process or project. It is ironic that such discipline and due diligence is not applied to the execution of the Lean Six Sigma deployment process itself.
For various reasons, the excitement and momentum around a deployment often begins to wane around a year to 18 months into the effort. However, waiting until a year into a company’s deployment to determine whether it is on the right path – and the program is being executed as planned with the desired results – is not a recipe for success.
A Lean Six Sigma deployment should be approached like any other strategic initiative; it should have a detailed plan that links the Lean Six Sigma tools, usage and desired culture shift to the business strategy. Then the organization needs the discipline to execute the plan. Adherence to the deployment plan can be audited, observed and measured in several ways. Measuring a Lean Six Sigma deployment against a hierarchy of success may occur a number of times:
- During initial training phases and project implementation waves.
- At the level of impact on specific processes.
- Or, holistically through an audit against the stated goals of the deployment itself and in comparison to norms exhibited in the best practices of other Lean Six Sigma deployments outside of that organization.
Apply Formal Evaluations of Training and Projects
How does a company gauge project work effort/accuracy?
To ensure successful knowledge transfer and the meeting of established accreditation requirements, the company should track two sets of metrics – knowledge transfer and project results in terms of verifiable financial benefit.
Knowledge transfer metrics can be weekly training quizzes that allow experienced Master Black Belts to understand if critical concepts are being understood by program participants. If not, then it allows instructors to identify participants or groups of participants that may require additional coaching or training on specific tools or concepts.
Project result metrics ensure that participants can translate their training experiences into projects results. This can be tracked through dollars realized, project cycle times and schedule slippage. In addition, project results should be checked several months post-Control at the “validate gate” to ensure project results are being sustained. Since these metrics can be lagging indicators, Master Black Belt coaches can create project coaching reports to identify and address individual and systemic project issues.
A List of Deployment Sustainability Metrics
Additional enterprise-wide sustainability metrics include:
- Resource turnover and backfilling to maintain a critical mass of Black Belts and Green Belts.
- Quality and quantity of “project hopper” to ensure that Black Belts and Green Belts will have projects of value to customers/shareholders as soon as they complete their current project.
- Best practice leverage – How many best practice projects are being created? How often are these best practices being used?
- Transfer of knowledge and skills to Master Black Belts should be measured rigorously through a defined Master Black Belt development process.
When it comes to training, collecting meaningful feedback from attendees is vital. Knowing what works best will speed up the knowledge transfer and equate to better project results. Ensure that at the end of each training session, students are required to complete course evaluation and feedback forms, which ask at a minimum the following questions:
- Rate the effectiveness of this course (1 to 10) and provide comments.
- Did the course meet your expectations (Y/N) and provide comments.
- Rate the effectiveness of the exercises (1 to 10) and provide comments.
- Rate the effectiveness of the pre-work (1 to 10) and provide comments.
- Rate the effectiveness of the facilitators (1 to 10) and provide comments.
- Rate the effectiveness of the software products?
- What did you like best about this course? What did you like the least?
- What is the most important piece of knowledge you will carry back to your organization?
- If there was one thing that you could change about this course, what would it be?
- Other comments.
Each training session should be evaluated to determine immediate modifications or actions to take, as well as future modifications. Specific comments can be grouped, and root cause analysis performed to identify opportunities for both curriculum enhancement and instructor performance improvement.
Audits as a Powerful Tool for Improvement
Objective auditing and corrective actions are powerful tools which can be employed two levels within the organization, the specific process level and at the deployment/program level.
Auditing individual processes can evaluate internal operational process flows against business objectives and external business benchmarks. For example, can the human resources department fill open positions in X days as planned or needed? If not, then why not? Are the change-over times on the manufacturing floor consistent with manufacturer specs, company targets or industry benchmarks? If not, why not? Is the application-to-funding process at a bank branch faster or slower than other branches? If not, why not?
The key to these are defining what success looks like and then periodically auditing and observing the process performance to verify that is in within acceptable ranges. If an organization is not satisfied, then consider some quick fixes if the problem is clear or develop a project charter and offer it as a potential Green Belt or Black Belt project for future consideration.
The process audit approach focuses on verification of the manner in which people, procedures metrics, and enabling technology come together to produce an effective process output. A process audit compares and contrasts the manner in which customer requirements are met in relation to how the process was actually designed to meet them in the first place. The process audit also is concerned with the validity and overall reliability of the process itself. For example, is the process consistently producing acceptable results? Do non-value-added steps exist in the process? Are processes current in terms of meeting the customer’s existing and future requirements? Does the overall process complement the expressed or implied quality objectives of the organization – short-term customer satisfaction, long-term repeat business, continued profitability and growth?
Consider the Very Fabric of the Deployment
Similarly, audits also should be applied to the processes which make up the fabric of Lean Six Sigma deployment. These deployment audits are akin to process audits in that they look at process performance only in this case the processes are those which drive the deployment. They are conducted solely to diagnose specific performance related deployment deficiencies which upon discovery and correction will increase the return on the investment in Lean Six Sigma. The following areas should be considered when auditing a deployment:
Management Engagement: Have they made clear statements of vision for the deployment? Do they regularly support the deployment activities through words and deeds? Are they attending meetings and tollgate reviews? At what frequency? Are they setting the objectives? Are those objectives measurable? Are they strategic?
Deployment Planning: Does the company have a written deployment plan? Is it up-to-date? Is it being adhered to? If not, why not?
Communication Plan: Does the company have one? What are the elements or components? Is it being executed? Is it working? Is the organization reaching all employees and selling its successes?
Training Plan: Is the curriculum appropriate for company needs? What are attendance rates? Successful completion rates? Graduation rates? Test scores? Percentage which achieve certification?
Project Selection: Who decides what projects get executed? How is that decision made? How often should this group convene? Are they meeting as planned? What is the percentage of time the meeting is rescheduled or canceled? Is management attending regularly?
Project Execution/Certification: Project cycle times? Dollar value per project? Number of team members? Number of meetings/reviews? Completion rates? Reasons for drop-outs?
Documentation of Financial Benefits: To what extent is the CFO or financial controllers involved in the projects life cycle? Is someone signing off on the project benefits? What is the deployment’s ROI? (ROI = documented financial benefits – deployment expenses)
Deployments Like Organism: All Parts Must Function
A comprehensive deployment audit that covers the outlined areas above is doing more than measuring training or a single process out of context. This systemic audit allows the company to look objectively at whether the overall program is on track to achieve its stated goals.
There is a lot more to a sustainable deployment than simply executing projects. Successful deployments are always those with what some consider peripheral or support activities like personnel certification, communication plans, and rewards and recognition. What is often misunderstood is how important these functions really are in creating and keeping sustainable momentum. Successful managers understand that deployments are like a living organism with multiple parts to function properly. If project execution were the heart of the deployment then other functions serve no less important roles than that of the liver and the kidneys.
Deployment leaders and general management will greatly increase their return on their investment in Lean Six Sigma by applying continuous improvement techniques such as specific process and deployment audits to their own deployment.