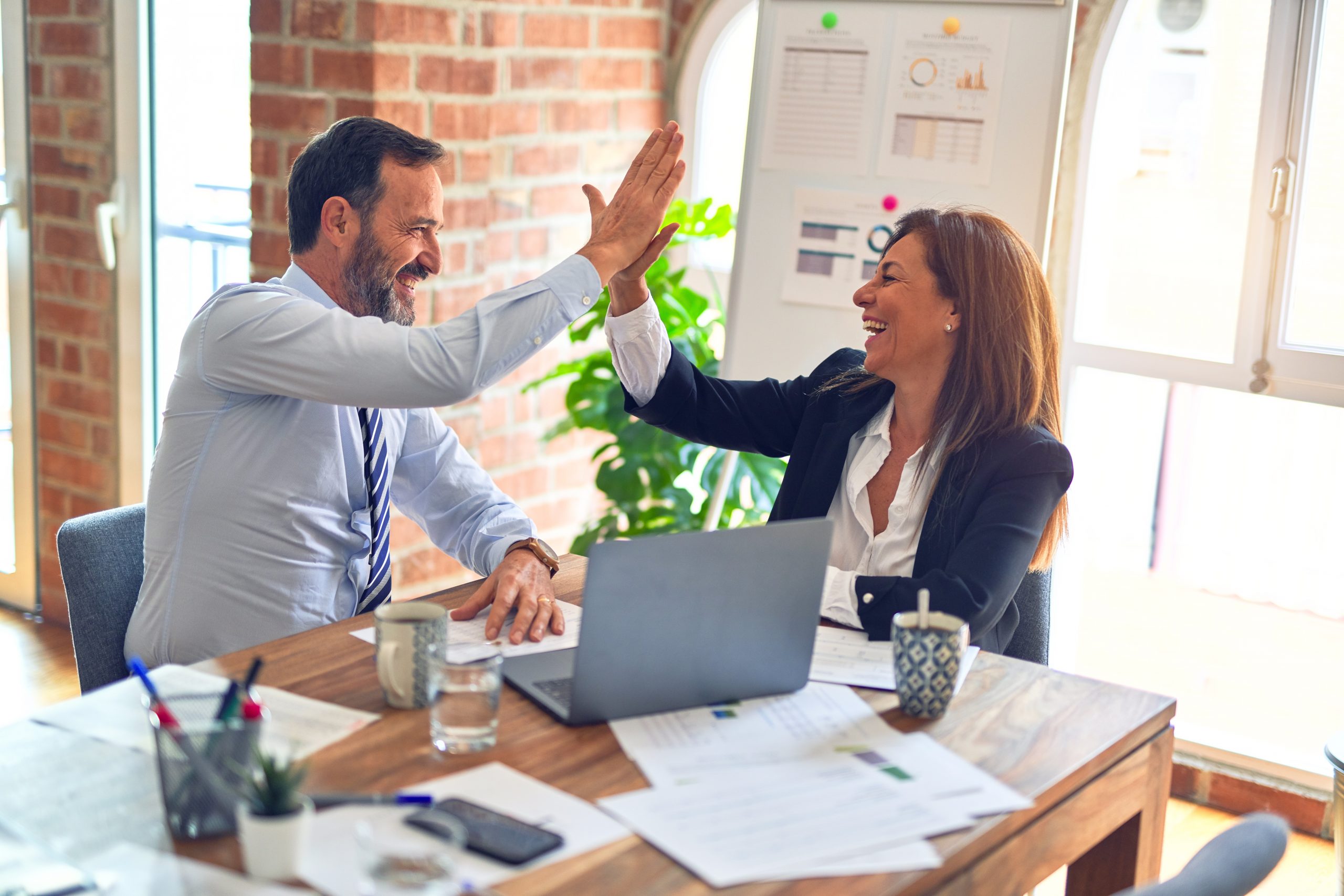
Making changes in an organization, especially when embarking on a new improvement method such as Six Sigma, can be slow going – employees may see the method as “just another fad.” Because of this, leaders need to use a deployment approach that will kick-start a change program, and keep it maintained.
One method to approach the change is to actively engage process owners. This can be done through the creation of standards for how a process is to be completed, using owner input. Standards can be a helpful tool for practitioners who feel the people in their organization are not fully bought into a new full blown change program or who feel they do not have the time to put in a complete change program, but still wish to reap benefits.
Achieving Consistency
For any process, if there is more than one person completing it, there is likely to be more than one method used. This has the potential to cause issues with the consistency of output and consistency of training. One way to overcome these issues is to work with process owners to standardize the process, ensuring that each time the process is required, it is completed in the same way.
The benefits of having a standard process are that the organization can be more certain about achieving a consistent output from the process. The method can be rolled out for new employees, thus continuing the consistency of output. Also, the internal audit department or outside regulatory bodies are more likely to be satisfied with the standard process than one that could be completed in a variety of ways. And once a standard process is implemented, it can be a springboard for further change in the future.
Setting the Standard
To begin standardization, practitioners need to create a process map with the steps to complete the process. This information is gathered using the knowledge of the people actually involved in performing the process. Keep in mind, this map may not be the same as the way the manager thinks the process is completed or the way the process should be completed. This will be a warts-and-all description of what really goes on at the front line.
As it becomes apparent that there are certain sections within the process that are completed differently, the people gathered together will need to decide what is the most efficient way of completing that step. At the end of this discussion, the best way of working – as advised by the people doing the work – will emerge.
The process map of the standard way of working should then be turned into an operating manual. This paper or electronic copy can be used when training new people, or for reference by auditors or regulatory bodies. It can also be used when reviewing people’s performance against the standard.
Reaping the Benefits
By mapping out standard processes and turning them into operating manuals, an organization can achieve two things: a solid base on which to make some improvements and a working manual that should be updated when further changes are made. If the standards are followed, increased productivity, improved quality and reduced costs also can be expected.