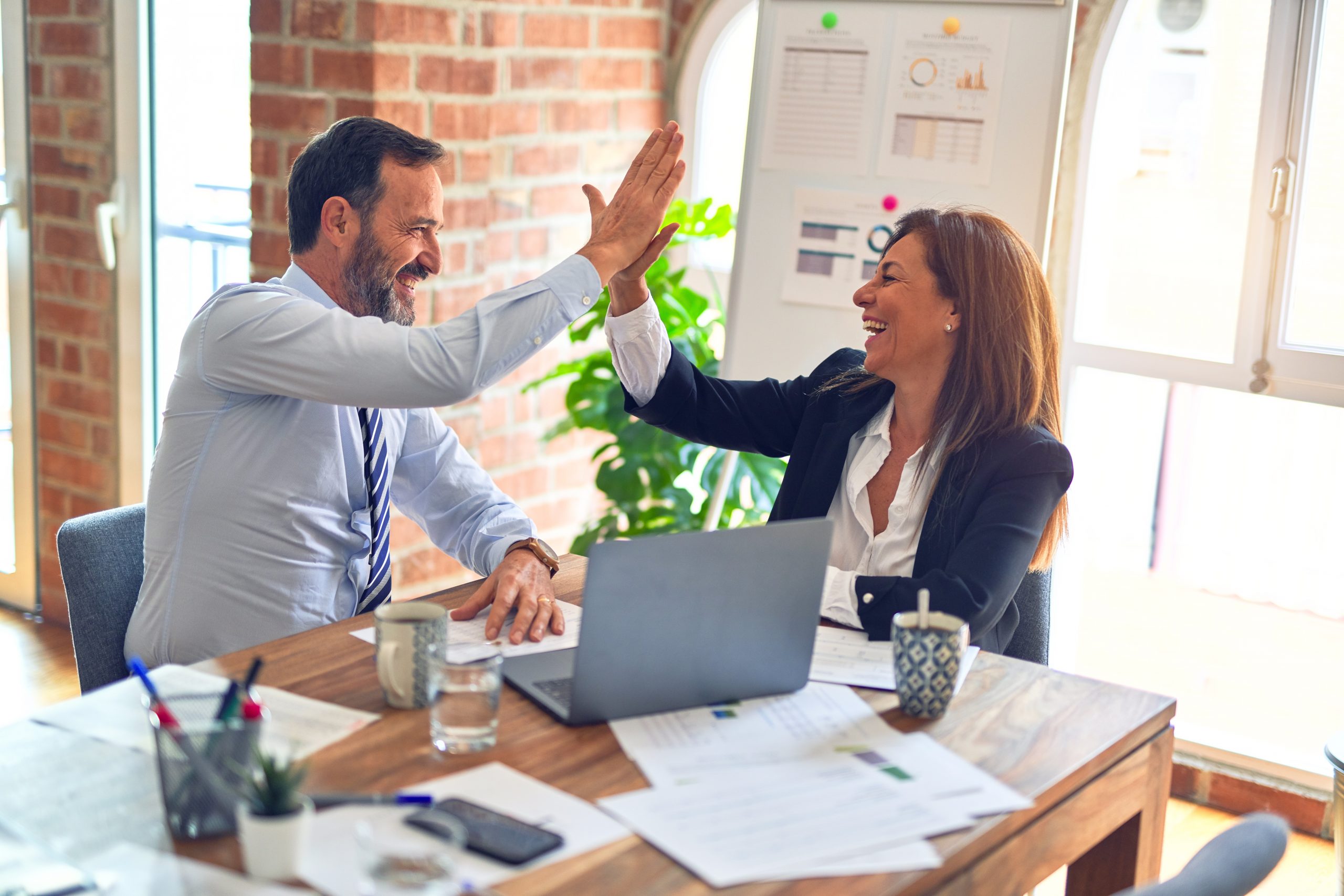
Until relatively recently, many quality professionals considered the term “Lean” to only be applicable to the manufacturing giants of industry. Lean, first created as a part of the Toyota Production System, is an operational approach and methodology embraced by world-class companies around the globe. With proven results, Lean has made its way into non-manufacturing industries, such as insurance, banking and even healthcare.
The manufacturing industry had many skeptics in the late 1980s and early 1990s who initially thought Lean would be just another buzzword or management fad, joining such flashes in the pan as total quality management and re-engineering. A decade later the proven Lean principles have withstood the test of time. Their success stems from the relentless efforts of Lean practitioners to eliminate or drastically reduce waste that adds no value for customers. When done right, Lean ultimately permeates all that an organization does.
Lean Being Applied in Healthcare
Now Lean is being applied with resounding success in the healthcare industry. Unfortunately, Lean is a term that is still foreign to many in an industry that is fraught with skyrocketing costs, poor patient (customer) and caregiver (employee) satisfaction, complex and cumbersome IT solutions, nursing shortages, physician frustration and malpractice cases resulting from inadvertent errors and oversights. Nonetheless, the basic principles of Lean are tailor-made for the healthcare industry, which is made up of many manufacturing-like processes but has always struggled to evaluate those same processes like the “metal-bending” industrial sector.
One reason the Lean practices are somewhat foreign to many in healthcare is apparent to experienced Lean practitioners. Many other industries have attempted to drastically improve their processes with increased automation and software alone. Some in the healthcare industry are following the same path today. Many of the necessary tasks required in today’s healthcare sector are inefficient, if not impossible, without a solid IT platform, but despite the importance of such systems, they cannot be looked to as a cure for all the operational issues that plagues this industry.
Recently one healthcare organization had a goal to decrease its turnover time in the operating room. The use of Lean tools eliminated waste, idle time and efforts that added no value from the patients’ or physicians’ perspective. Additionally, visual indicators were put in place to help reduce errors and rework. The team for this project was able to immediately reduce the turnover time by 50 percent – with minimal investment and without any changes to the hospital or departmental IT systems.
Lean Tools Have Healthcare Applications
In a Lean organization, processes and value streams associated with services, products and patient care are continually evaluated for waste. Such waste is then attacked with a vengeance using a number of industry-proven tools, such as:
- Pull systems and “flow” to improve throughput in areas such as labs and other places with paperwork-intensive processes.
- SMED techniques applied to changeover time improvements in operating rooms. (SMED comes from the manufacturing industry and stands for “single minute exchange of die.”)
- Poka-yoke, aimed at reducing the opportunity for errors and omissions.
- 5-S, used to rearrange/reorganize nursing stations and other healthcare workplaces for greater efficiency.
Lean is not intended to target changes in the clinical medical procedure or nursing care. Lean also is not intended to eliminate employees. Lean’s only objective is to eliminate waste in all tasks and processes that provide no value so that more time can be dedicated to patient care, which in Lean terms is value-added in the eyes of the customer.
While Lean is not the solution for every problem faced in the healthcare industry, or any other industry for that matter, it can certainly make some dramatic improvements that provide sustainable and employee-embraced positive change. Whether a clinician or a patient, many agree that such improvements are needed in order to contribute to physician, employee and patient satisfaction.