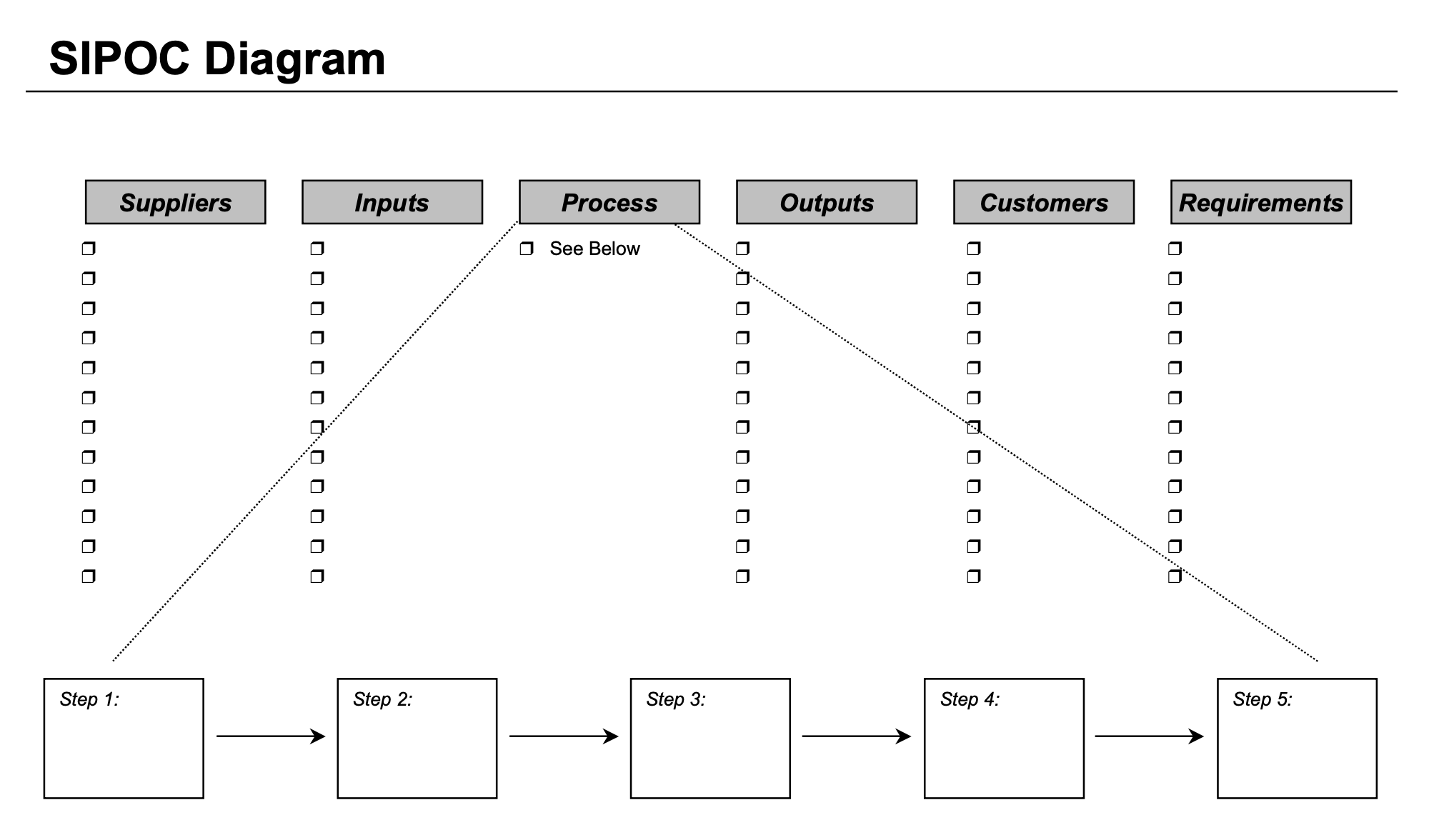
Many recent inquiries and discussions have focused on the SIPOC diagram – a tool used in the Six Sigma methodology. Because of the interest level, a further explanation is presented here along with a sample and template for your use.
A SIPOC diagram is a tool used by a team to identify all relevant elements of a process improvement project before work begins. It helps define a complex project that may not be well scoped, and is typically employed at the Measure phase of the Six Sigma DMAIC (Define, Measure, Analyze, Improve, Control) methodology. It is similar and related to process mapping and ‘in/out of scope’ tools, but provides additional detail.
The tool name prompts the team to consider the suppliers (the ‘s’ in SIPOC) of your process, the inputs (the ‘i’) to the process, the process (the ‘p’) your team is improving, the outputs (the ‘o’) of the process, and the customers (the ‘c’) that receive the process outputs. In some cases, requirements of the customers can be appended to the end of the SIPOC for further detail.
The SIPOC tool is particularly useful when it is not clear:
- Who supplies inputs to the process?
- What specifications are placed on the inputs?
- Who are the true customers of the process?
- What are the requirements of the customers?
Sample SIPOC Diagram
A SIPOC diagram is a tool used by a team to identify all relevant elements of a process improvement project before work begins. It helps define a complex project that may not be well scoped, and is typically employed at the Measure phase of the Six Sigma DMAIC methodology.
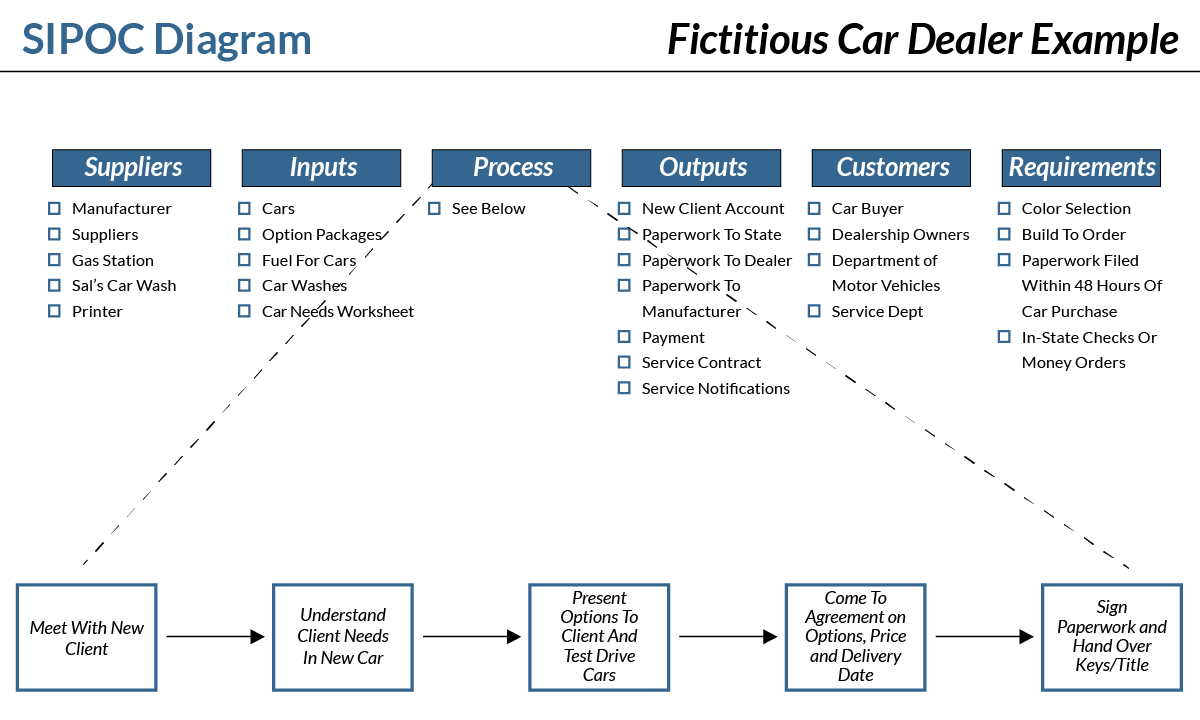
Steps to Complete the SIPOC Diagram
SIPOC diagrams are very easy to complete. Here are the steps you should follow:
1. Create an area that will allow the team to post additions to the SIPOC diagram. This could be a transparency (to be projected by an overhead) made of the provided template, flip charts with headings (S-I-P-O-C) written on each, or headings written on post-it notes posted to a wall.
2. Begin with the process. Map it in four to five high level steps.
3. Identify the outputs of this process.
4. Identify the customers that will receive the outputs of this process.
5. Identify the inputs required for the process to function properly.
6. Identify the suppliers of the inputs that are required by the process.
7. Optional: Identify the preliminary requirements of the customers. This will be verified during a later step of the Six Sigma measurement phase.
8. Discuss with project sponsor, Champion and other involved stakeholders for verification.
The SIPOC diagram is an essential tool for teams embarking on process improvement projects, especially when there’s ambiguity regarding the project’s scope. By breaking down the process into its core components, teams can gain a holistic view of the entire system. This ensures that no critical element is overlooked. Furthermore, by identifying the suppliers, inputs, processes, outputs, and customers, teams can pinpoint potential bottlenecks, inefficiencies, or misalignments in the existing process. Engaging stakeholders, such as the project sponsor and Champion, in the SIPOC creation process ensures that the team has a comprehensive understanding and alignment on the project’s objectives and deliverables.
Key Points About SIPOC
- What is SIPOC? A tool used in the Six Sigma methodology to identify all relevant elements of a process improvement project.
- Components of SIPOC:
- Suppliers (S)
- Inputs (I)
- Process (P)
- Outputs (O)
- Customers (C)
- Purpose: Helps define complex projects that may not be well scoped, typically used in the Measure phase of Six Sigma DMAIC.
- Benefits: Clarifies suppliers, input specifications, true customers, and customer requirements.
- Steps to Complete: Start with mapping the process, then identify outputs, customers, inputs, suppliers, and optionally, preliminary customer requirements. Verification with stakeholders is crucial.